
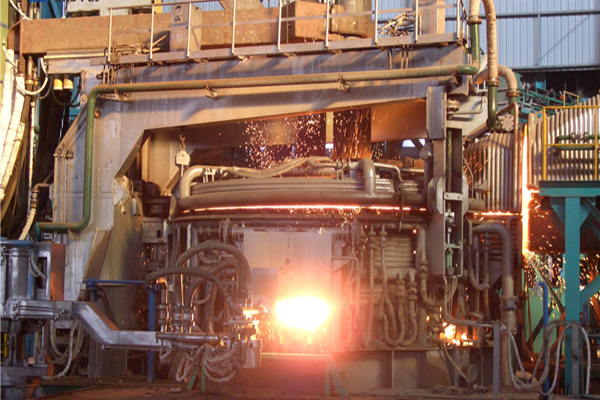
But making it is an incredibly polluting process, with the industry responsible for 8% of the world’s CO2 emissions. It’s also critical to building renewable energy infrastructure like wind turbines, which the world needs in order to eliminate fossil fuels. Steel is among the most important materials in modern society, going into everything from buildings and bridges to cars and bicycles. Last summer, the facility produced iron for the world’s first fossil-fuel-free steel, blazing a trail towards decarbonizing one of the world’s most heavily-polluting industries. But SSAB’s HYBRIT pilot plant-built in collaboration with Swedish state-owned mining company LKAB and state-owned power company Vattenfall-emits nothing but water vapor when it refines iron ore.

Traditional blast furnaces emit huge amounts of CO2. It’s spectacular in a different way, though. “You don’t see very much either, because it’s all automatically-controlled.”

“It doesn’t look that spectacular,” says Martin Pei, executive vice president and chief technology officer at the Swedish steelmaker.
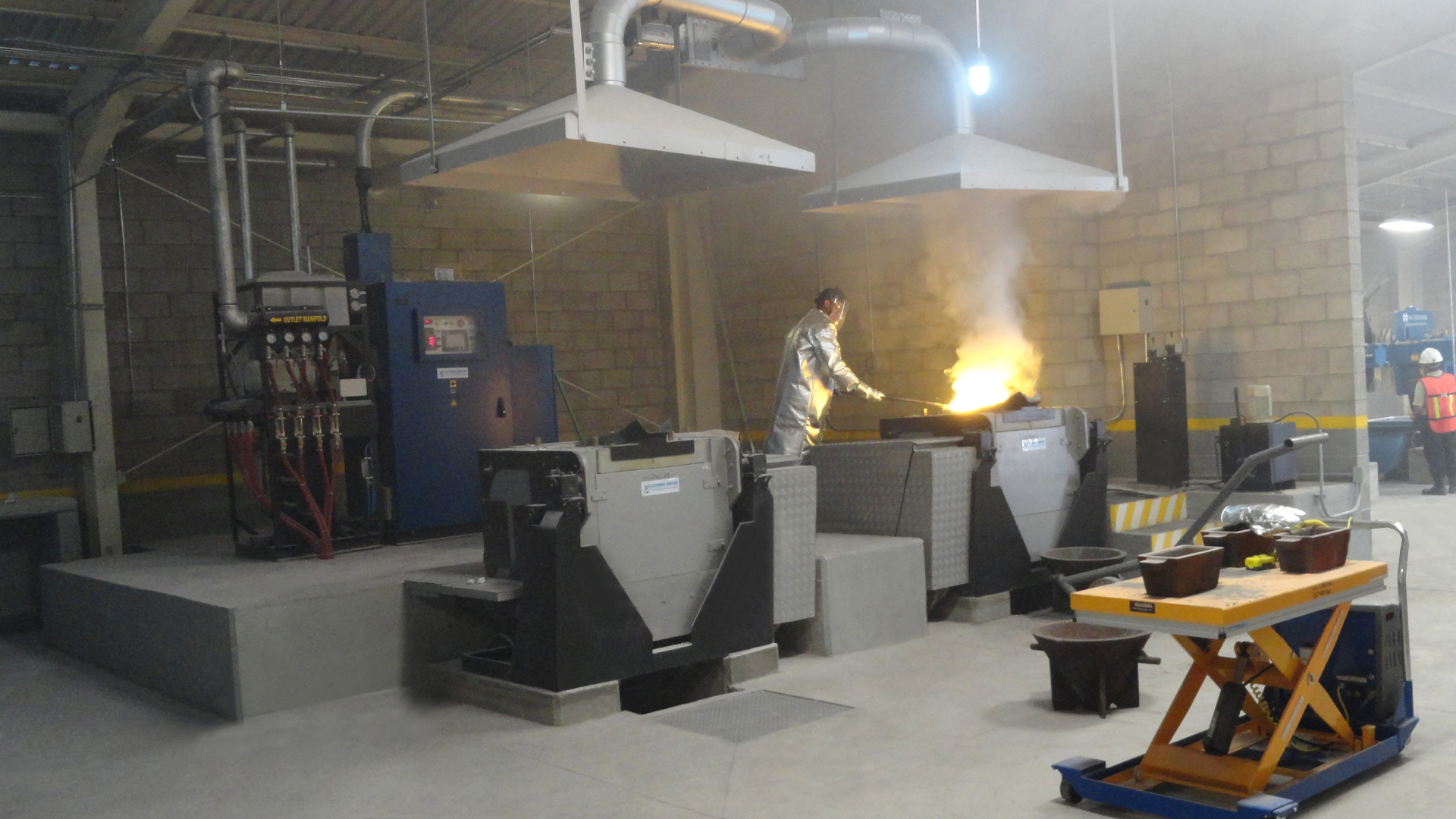
Tokyo Steel Kyushu Works issued a Preliminary Acceptance Certificate to confirm the completion of commissioning in accord with a narrow contractual schedule.At a steel plant in Lulea, Sweden, workers make the world’s most essential construction material the old fashioned way: piling iron ore and coke, a kind of coal-derived fuel, in a huge blast furnace, heating the mixture to enormous temperatures, and then “tapping” the cauldron of molten metal, which sends a stream of white-hot pig iron-and showers of sparks-spilling out along a sluiceway.īut less than a mile away, the plant’s owner, SSAB, is piloting a less dramatic steelmaking process at a new facility. In addition, this digital solution ensures compliance with the flicker limits and the harmonic distortion thresholds imposed on the grid by the electricity supplier. The power-on time was decreased to an average of 22 min and the power factor is higher than 0.96, compared to the previous 0.90.Įlectrode saving at 40 Hz is in the order of 10%, compared to the previous analog operation.įrequency of operation is foreseen to move down to 30 Hz and less in the next days to introduce more operation savings. The variation of the fundamental frequency of current is dynamically possible only thanks to the innovative Q-ONE and creates a capability to reach and set new targets for the steel industry. The energy consumption recorded at different frequencies, based on the same Delta Temperature (ΔT), has shown that at 40 Hz it is possible to obtain an electrical energy savings of 12% compared to the refining process without the Q-ONE.
#Electric arc furnace startup time full
The full system was installed in just 20 days during the summer production shutdown, as crews worked on three shifts to reach the challenging target. The patented Danieli Automation Q-ONE technology already used by European steelmakers is in operation now at the Tokyo Steel Kyushu plant, in Japan.ĭesigned with a single, high-current power unit for the 115-t ladle furnace and working with currents up to 25 kA and 205-V arcs, the Q-ONE successfully processed the first heat on August 12, 2021.
